Duct leakage is a major source of energy loss in residential buildings. Most duct leakage occurs at the connections to registers, plenums, or branches in the duct system. At each of these connections, a method of sealing the duct system is required. Typical sealing methods include tapes or mastics applied around the joints in the system. Field examinations of duct systems have shown that taped seals tend to fail over extended periods of time. The Lawrence Berkeley National Laboratory (LBNL) has been testing sealant durability for several years. Accelerated test methods were used that continuously expose duct sealants to elevated temperatures (200 to 212F (93 to 100C)). We found that typical duct tape (i.e., fabric backed tapes with natural rubber adhesives) fails more rapidly than all other duct sealants. We also tested advanced tape products being developed by major manufacturers. The results of these tests showed that the major weaknesses of the tapes that fail are the use of natural rubber adhesives and the mechanical properties of the backing. The test results also showed that the current UL listings are inadequate for indicating durability and many tapes showed significant failure when testing using UL 181 B-FX procedures. In addition, the clamps required (but not evaluated) by UL-181B-FX had many failures and their durability also required evaluation. An accelerated test method developed by LBNL is being used as a basis for an ASTM standard under sub-committee E6.41.
Advanced Duct Sealant Testing
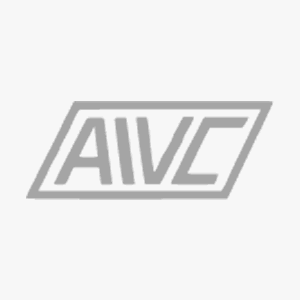
Year:
2003
Bibliographic info:
LBNL - Indoor Environment Department Publications, LBL