An approach to the steady-state simulation of heat pumps and refrigerating equipment is presented. Novel features of the proposed model are the strategy and formalism adopted in the programme development. Individual mathematical models for component design are linked to enable the simulation of a basic vapour compression cycle. This paper introduces some of the component modules, which can be used for pure as well as mixed refrigerants. Because numerous models can be used for a specific piece of equipment making up the whole refrigerating/heating unit, the Modular Modelling approach leads to a flexible and evolutive structure. A machine can actually be built-up from component libraries that include several types of heat exchangers, compressors and expansion devices and the effects of operating conditions or component geometrical parameters on cycle performance can be examined. Because actual test data are used to "calibrate" the component modules, very accurate results are obtained. The proposed model is validated with experimental results from an air-to-air split unit using R22 and a water chiller using R22 and R407C. Discrepancies smaller than 5% are obtained on the cooling duty and COP of the split unit and the chiller components.
Design and simulation of heat pumps and A/C equipment using pure and mixed refrigerants with MoMo (Modular Modelling)
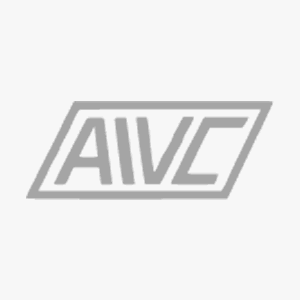
Year:
1997
Bibliographic info:
Belgium, Proceedings of Clima 2000 Conference, held Brussels, August 30th to September 2nd 1997