We investigate optimal supervisory control of a building energy system with cogeneration of heat and power (CHP). The system consists of a Stirling engine and a supplementary burner, space heating and a domestic hot water (DHW) storage tank. Cost and primary energy (PE)-optimal operation are considered.
The best theoretically possible operating strategy is found using the following assumptions:
An ideal dynamic model of the system and an ideal prediction of all future disturbance variables (weather, hot-water draws, etc.) are available to the controller (ideal here means that model and predictions used by the controller perfectly match reality, which is used for simulation after applying the control signals)
The room temperature is allowed to vary within a time-dependent tolerance band (e.g. 21...24C during the day and 19...24C at night). Progression of the room temperature is then an output of optimization. A dynamic building model is used, rather than heat demand profiles. A similar tolerance band is used for the DHW storage tank
This strategy defines the so-called performance bound, since no real controller can yield a better performance. It is found using model-predictive control (MPC) with moving horizon.
In this general setting, the following results are discussed:
Control strategy: How does the system have to be operated to cover thermal and electrical energy demand with minimal costs, or with minimal PE?
Performance assessment: What annual amount of primary energy and money can be saved by a CHP unit compared to conventional heating?
Influence of specific parameters (sizing of Stirling engine)
The results, although obtained with a Stirling engine, can be used for other CHP units as well.
Optimal Control of Cogeneration Building Energy Systems
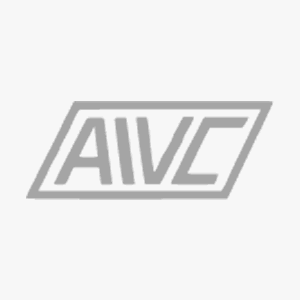
Year:
2007
Bibliographic info:
Proceedings CLIMA 2007 - Wellbeing Indoors (10-14 June Helsinki)