A numerical model, employing a local-averaging formulation was developed for heat transfer and water vapor deposition within fiberglass insulation under air exfiltration and frosting conditions. Frost growth on the cold surface was modeled using special frost growth boundary conditions. Non-isotropic permeability effects that occur in fiberglass boards were included in the mode/for porous medium flow because tests showed that the permeability for flow parallel to the plane of the boards was 69% higher than perpendicular to the insulation boards. Transient heat and moisture transfer processes within a thick layer of fiberglass insulation were modeled for steady exfiltration of humid air (60% to 84% rh) with a two-dimensional airflow during winter temperature conditions. In order to validate the numerical model, laboratory apparatus was constructed with a test cell I 35 mm high, 600 mm wide and 275 mm deep. This allowed a two-dimensional moist air exfiltration [0.5 to 1.5 L(m2.s)] through a fiberglass insulation slab for a temperature range - 20 °C to 21.5 °C from the cold outside surface to the warm inside surface. Using this apparatus, the transient temperature profiles, moisture accumulation profiles, and heat-flux at the cold side of the fiber-glass insulation were measured during the air exfiltration process. Part I outlines the theoretical/numerical model and describes the experimental test facilities and the properties of the fiberglass insulation tested. Part II of this paper presents the comparisons of experimental data and corresponding simulation results.
Two dimensional air exfiltration and heat transfer through fiberglass insulation. I. Numerical model and experimental facility.
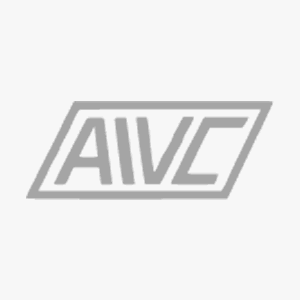
Year:
1997
Bibliographic info:
Int. J. HVAC and R Res., Vol 3, No 3, 1997, pp 197-213